ELEPOT
Applications
- 1 Quenching, tempering and annealing of steel
- 2 Melting and sintering of metal
- 3 Heating for shrink-fit and processing
- 4 Solution heat treatment, stress relief treatment, aging heat treatment
-
5
Other heat treatments
Compatible with a wide range of temperatures up to 1150℃ (It can be set in 1℃ units)
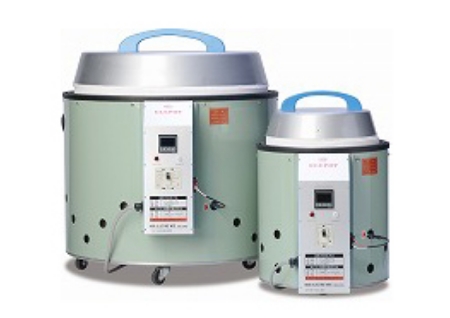
FEATURES
-
1 Low price
Mass production by mold forming has allowed us to offer the lowest price of the industry.
-
2 It can be installed anywhere with amazing lightness
One-piece ceramic fibre into the thermal insulation and providing air layer be-tween outer wall, its designed as light movable furnace by our weight saving technology. Click here for details on miniaturization and weight reduction.
-
3 Energy-saving electric furnace
Heats up with 1/3 the power of conventional furnaces. Reached 1150℃ with 1.8kW power. (for SH type)
-
4 Commitment to shape
The cylindrical shape enables to get work heated evenly. Also its designed with the lid witch allows easy loading/unloading of work as well as increasing effi-ciency.
-
5 User-friendly simple operation
It is a simple operation just set the temperature and timer. The temperature con-troller has a built-in timer and issues a buzzer alarm after the holding time. Three-level P.I.D.control provides stability and accuracy of temperature setting.
-
6 Built-in safety feature to prevent overheating included
It automatically turns off the breaker and shuts off the power in case of emer-gency for excessive temperature rise. (ELEPOT “LU model” is exception)
Demonstration of ELEPOT
Built-in Features
Model | Small Size | Large Size | Ultrahigh Temperature | |
---|---|---|---|---|
SL Model | SH Model | LH Model | LU Model | |
Maximum Temperature | 1050℃ | 1150℃ | 1150℃ | 1400℃ |
Regular Temperature | 1000℃ | 1100℃ | 1100℃ | 1300℃ |
Power Requirement | 100V 1.3KW | Single-Phase 200V 1.8KW | Three-Phase 200V 4KW | Single-Phase 200V 4.5KVA |
External Dimensions *1 | ø355×540mm | ø620×700mm | 500×500×820Hmm | |
Internal Dimensions | ø200×300mm (275mm)*2 | ø400×400mm (370mm)*2 | ø200×320Hmm (310mm)*2 | |
Throughputs (bottom reinforcement) | 5kg or less (inapplicable) | 10kg or less (30kg/50kg or less) | 5kg or less (inapplicable) | |
Net Weight | 15kg | 40kg (with caster) | 66kg |
*1 Excluding control panel *2 Furnace effective dimensions
Please feel free to contact with us about voltage change and process control specifications based on your needs.
The following parts are included.
Hearth plate x 1, Heat-sensitive bar x 1, Lid table x 1, Repair cement x 1, Liner piece x 4 (small) / x 8 (large)
●Outlet plugs are not included with the SH, LH and LU types. Please prepare a plug with the shape that fits your region.
●The set temperature will be held as is after the temperature holding end buzzer stops.
●We recommend ultra high temperature LU model for the operation that requires more than 1100℃ (for quenching, sintering of high-speed tool steel, etc.)
Ultrahigh Temperature Electric Furnace “ELEPOT LU Model”
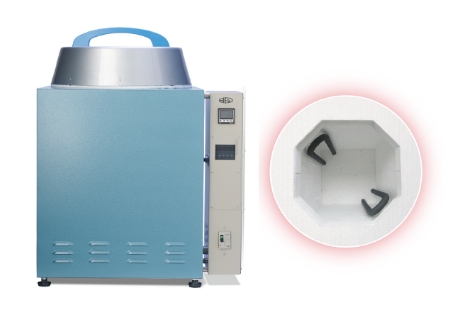
The ELEPOT LU model is designed to operate with higher temperature, that can handle up to 1,400℃. It uses a SiC (silicon carbide) heating element (* 1) for heater and can be operated stably over a wide temperature range. It is equipped with the same temperature controller as the conventional ELEPOT and can be simply operated just by setting temperature and timer.
* 1 About SiC (silicon carbide) heating element
The electrical resistance of SiC (silicon carbide) heating element gradually de-creases from normal temperature to around 800-900℃, on the contrary, at high-er temperature increases the electrical resistance. Therefore, it uses a special thyristor (SCR) that can automatically adjust the current to keep the temperature constant and it enables automatic and stable temperature control.
The life of silicon carbide in the heater is shortened because the oxidation pro-ceeds rapidly in the presence of water vapour. Also, be careful when using alka-line solution, chlorine, sulphide gas and so on, because erosion occurs and the life is shortened. If you expect to use under such special conditions, please con-tact us as you can change to heaters with various coatings.
When used for a long time, oxidation gradually progresses, and the electrical re-sistance increases due to the generation of silicon dioxide (silica). Please note that the heater weakens as service life approaches and It will crack and make it easier to spark. It may also shorten the life of the electric furnace. Therefore, we recommend to replace the heating element when the electrical resistance be-comes three times the initial value.
Secret of miniaturization and weight reduction of ELEPOT
ELEPOT is compact and light
“Compact and light” is one of the features of ELEPOT. The weight is only about 15kg for small model and about 40kg for large model (with caster). Therefore, there is no need to hassle when installing or moving the workplace since it is eas-ily to move and carry.
“Air Layer” is the key
The “air layer” is a key for our miniaturization and weight reduction. Since the outer wall of the furnace would become hot and dangerous if the heat insulation material was thin, usually more heat insulation material is equipped and it in-creases the weight. However, ELEPOT has an outer wall attached to the outside of the outer wall with an air layer in between, and it allows the outermost wall to be at a safe temperature with less insulation.
Thermal conductivity of air
Iron = 84 (W / mk), Ceramic board = 0.3 (W / mk), Air = 0.024 (W / mk).
Referring to the thermal conductivity (* 1), You can see that the air hardly trans-fers heat, and utilizing this property enables us to reduce the size and weight of the ELEPOT. Also the specifications are satisfactory even for professionals be-cause of the detailed design such as heat storage and heat dissipation of the heat insulating material and repeated heat resistance tests.
Thermal conductivity (* 1) refers to the speed and ease with which heat is trans-mitted.
A numerical value that shows how much heat is transmitted when there is a tem-perature difference of 1℃ between both ends of a 1m thick plate. The smaller the value, the higher the heat insulation performance.